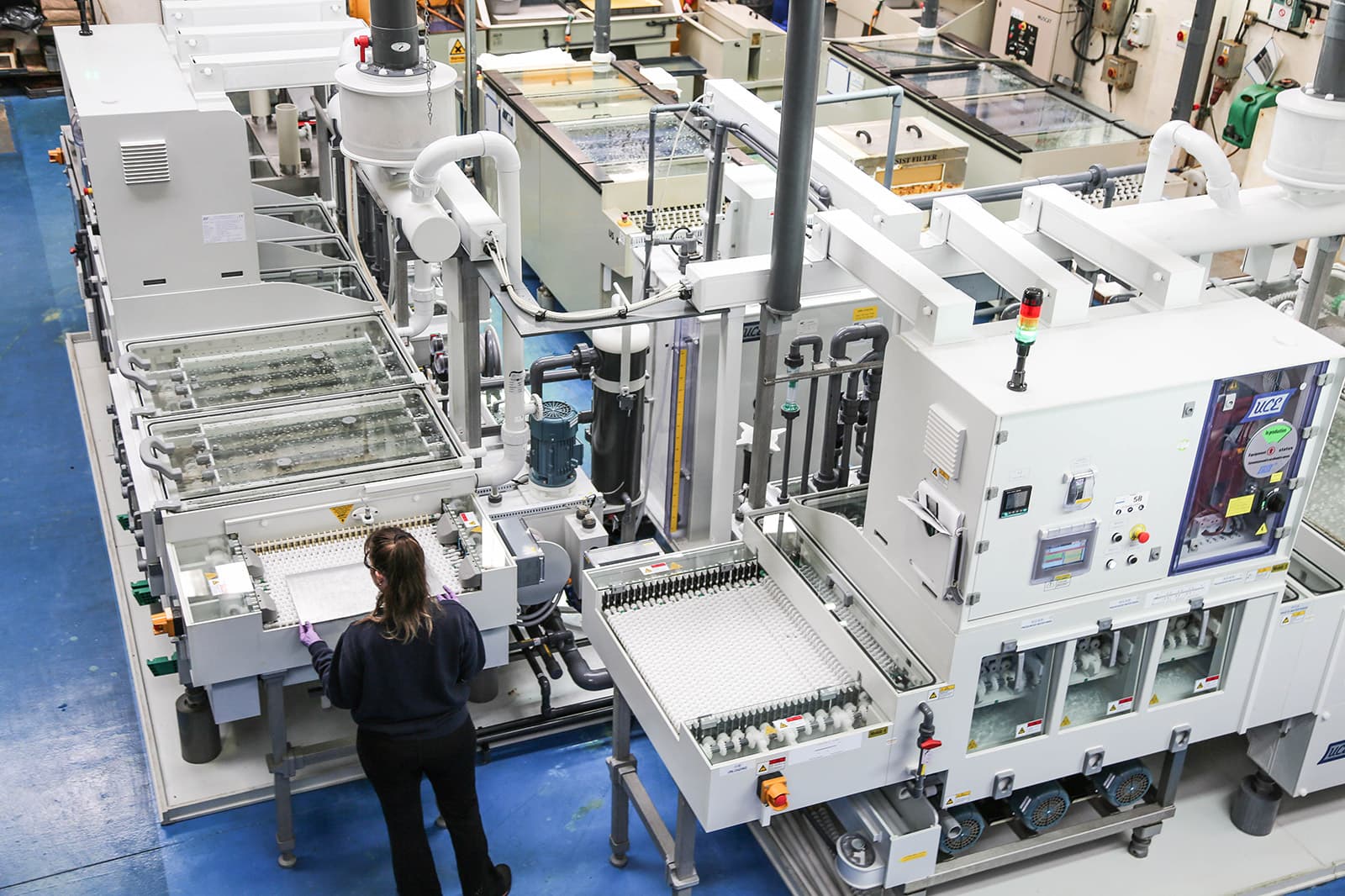
Advanced Chemical Etching Ltd (ACE) has recently completed a £600,000 investment programme at our West Midlands manufacturing facility, refining our chemical etching process, reducing our already short project lead-times and increasing capacity by 100%.
This increased investment passes on significant benefits to our customers – new technology, inspection equipment and a focus on automation means that we remain leaders in precision components manufacturing, and can continue to offer the highest quality chemically etched products at the very best prices.
Our increased capacity gives us the edge when responding to emergency turnaround jobs – our customers in the Automotive, Aerospace, Electronics, Precision engineering, Medical and Renewables sectors enjoy the confidence of knowing that all components will be produced with the same precision and attention to detail they have come to expect – now with timescales further reduced thanks to reduced machine downtime and even more efficient supply chain management. We are now capable of photo etching 2000 sheets per day in a range of metals, including Stainless Steel, Aluminium, Aluminium Bronzes, Copper Alloys and Titanium at a range of thicknesses.
No matter your requirements, our expert team will work with you to produce the high performance, lightweight and reliable parts you need. Contact ACE today on +44 (0)1952 416 666 or email sales@ace-uk.net for an initial consultation.
Our benefits at a glance
- New auto lines in front end (pre-clean, developing, stripping and post cleaning) fitted with auto dose units so chemistry additions are controlled (not down to operator interpretation)
- Capacity and expertise to pick up emergency turnaround jobs
- Additional inspection equipment CMM for 3D dimensional validation and 3D microscope for inspecting surface roughness and micro etched channel shapes
- Less machine downtime due to new process control procedures developed in lab for more consistent chemistry including inhouse XRF chemistry certification
- LED imaging of digital tooling for fine line imaging and now capable of parts 600mm x 1500mm and capacity of many ones, thousands or millions.
- New production management boost to bring world class customer service levels to ACE customers (Plant & Facility Manager for Preventative Maintenance and Automation Expert, Production Manager to focus on Leadtime and Customer satisfaction & Quality Manager to bring highest levels of quality & accreditations in Aerospace, Automotive & Medical fields.
Materials we work with
- Aluminium 0.025mm – 2.5mm – (all grades including clad, aluminium bronze and aluminium coated kapton)
- Copper Alloys 0.025mm – 2.0mm – (including all grades of brass, beryllium copper, copper, nickel silver, phosphor bronze, high performance coppers)
- Titanium Alloys 0.025mm – 1.00mm – (including all alpha, beta and nitinol grades)
- Stainless Steels 0.005mm – 1.5mm – (including all Austenitic, Ferritic, Martensitic, Low & High Carbon Steels.