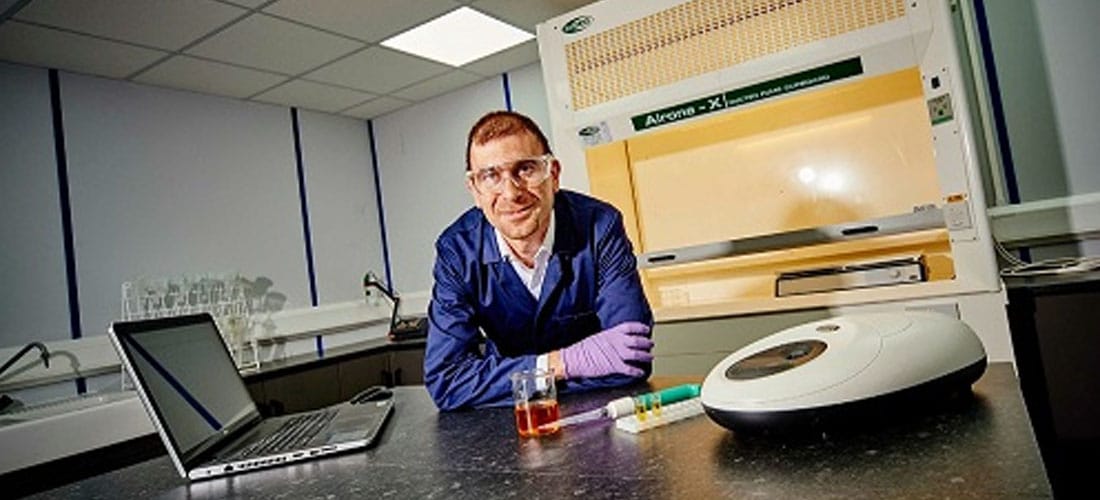
£150,000 investment in a state-of the-art laboratory and new metrology department is already paying off for a Telford manufacturer after securing a string of new aerospace and medical contracts.
Advanced Chemical Etching (ACE), which produces precision metal components, has landed more than £500,000 of orders thanks to its ability to offer access to new etching chemistry and expertise in aluminium, titanium and nitinol.
That has included supplying complex parts for aircraft engines, cabin interiors and landing gear applications, whilst medical customers have been tapping into the firm’s new capability for bone re-construction and bionic products.
Employing 46 people, the company is now looking to target more customers in these sectors and other industries that may be looking to optimise design and new material introductions to reduce weight and save costs.
“The new laboratory really puts us ahead of the competition and gives us the ability to develop safer chemistry processes and control tighter design parameters…delivering performance never seen in photo etching before,” explained Chris Ball, Director at ACE.
“In layman’s terms, it means we can offer customers the capability to ensure the quality of components for one offs/prototypes can now be transferred into the thousands normally found in mid to serial production.”
He continued: “Our aerospace and medical customers have been making the most of this new facility and the former now accounts for more than 40% of our turnover. There is now a significant opportunity to target F1, automotive and other high value engineering sectors who demand the same precision excellence.”
“One of the more advanced objectives completed was to come up with an etching process to corrode corrosive resistant materials, such as inconel and titanium.”
ACE’s scope of activities is far and wide and can include anything from safety critical components for aircraft and cars to simple washers, electronic connectors and ornate clock faces.
With the latest production machinery and a culture of continuous improvement at its 20,000 sq ft facility in Telford, it ensures it can make products in materials, including stainless steel, nickel alloys, copper, beryllium copper, phosphor bronze, brass and, thanks to ground-breaking new processes, aluminium, titanium, molybdenum, nitinol and elgiloy.
The company, which is working towards AS9100, has made a number of key appointments to cope with recent expansion, including a new technical sales specialist and business development expert.
Ian Whateley, Managing Director, concluded: “2016 is a major year for our business and we’ve really attacked the marketplace with investment in new technology, new capital equipment and new, highly skilled staff.
“We’re well on course to hit our business plan of turning over £5m by the end of next year.”